|
Kcon PMC Pvt. Ltd.
June 2013 |
 |
 |
|
Kcon PMC Pvt. Ltd. is a 25 years old design and engineering consultancy firm based in India. We specialize in water treatment systems and solid-liquid separation. We work in private, industrial, municipal and government sectors. Our founders have a cumulative experience of seventy years in this field.
We have to our credit about 600 plants around the world |
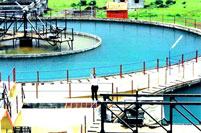 |
|
|
|
|
Ladivali, Dist. Raigadh, Maharashtra ( Figure ) |
|
This is a small Water treatment Plant for a dye manufacturing company. Raw water source is river patalganga. The raw water is
contaminated with industrial effluents. The average turbidity during
monsoon is 100-200 NTU, which peaks to 500 NTU during flash
flooding. The plant had original capacity of 30 m3 / hr. The treatment
units consisted of a Receiving chamber, Parshall Flume, Flash Mixer and
Sludge blanket type hopper-bottom settling tank.
The plant was augmented to capacity 100 m3 / hr in the year
1992. The existing inlet works were retained. A mechanical flocculation
tank with detention time of 35 minutes was provided between flash
mixer and settling tank. The settling tank was converted to a tube
settling tank with surface loading rate of 3500 lph/sqm. Entire plan area
of the tank was covered with tube modules, which were supported over
mild steel sections. New collection troughs with V notches were Provided in mild steel. The incoming flocculated water was distributed
at the depth of 1.5m below the tube modules with perforated
distribution pipes. This was done to change the predominantly vertical
flow pattern and to avoid possible disturbance to sludge blanket by
increase in the flow. Alum is used as a coagulant. Lime is dosed during
high turbidity period. Pre-chlorination is done in Receiving Chamber.
Clarified water turbidity achieved is between 5 to 10 NTU. As this was a
single stream �on-line� plant, shut down period for retrofitting of settling
tank was limited to 72 hours only.
During further expansion program undertaken by the company,
gravity filters were added to achieve treated water quality less than 1-2
NTU. Three new rapid sand gravity filter beds with rate of filtration 500
lph/Sqm were provided with an overhead backwash water tank. Due to
owner�s insistence on gravity filters, the clarified water was to be
pumped to filters as the FSL of existing clarified water storage tank was
barely 1.00 m above the ground. A new filtered water (pure water)
sump of adequate capacity was constructed with a pump house to
supply treated water to the factory.
There was enough redundancy provided in the process design
and hydraulics to further augment the plant capacity to 150 m3 / hr if
and when required. When operated at this rate, the detention time of
flocculator will reduce to 17.5 min, the loading on the Tube Settler will
increase to 5250 lph/sqm and rate of filtration will be 7500 lph/sqm.
The drive-unit for flocculator is capable of imparting the additional
energy to supplement higher velocity gradient. The Tube Settlers are
capable of handling the increase in surface loading effectively. The rapid
sand gravity filter beds will be converted into dual media filters by
replacing top portion of sand media with Coconut shell / Anthracite
coal. |
|
|
|
 |
|
|
|
|